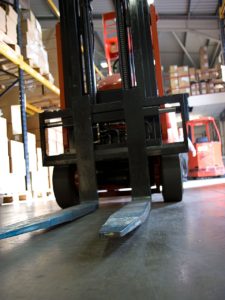
With businesses such as Ornua, Unilever and Johnson & Johnson all announcing plans to hold extra goods in the UK before Brexit Day, we look at stockpiling as a business strategy, its limitations and its likely impact on Europe’s supply chain in the coming months.
In a modern logistics environment where supply chains have been refined and purified over years of innovation, stockpiling should be a completely unnecessary option, but with the uncertainty around Brexit, many businesses have no alternative but to build it in to their contingency plans.
What are the benefits of stockpiling?
To cover any short-term supply chain issues in the first few weeks of Brexit, several FMCG, pharma and food businesses have started to build up extra stores of goods on both sides of the UK border. This strategy makes sense for manufacturers and distributors of non-perishable and temperature-controlled goods (brands like Kerrygold and Magnum) and for Pharma companies producing life-saving drugs like insulin and antibiotics. For the majority of manufacturers, distributors and retailers on either side of the UK border, however, stockpiling is just not a viable solution.
Fresh food can’t be stockpiled:
Many ambient perishable goods, like fresh fruit and vegetables, simply can’t be stored for long periods of time. Whilst stockpiling can be classed as a just-in-case business strategy (holding extra stock ‘in case’ it’s needed), fresh food is completely reliant on a functional just-in-time supply chain system — if delivery timelines can’t be met, goods decay and become worthless. What’s more, further down the supply chain, many small retailers lack the additional shelf space in their stock rooms to hold extra goods. In fact, the British Retail Consortium recently issued a statement confirming that shops can’t practically stockpile additional goods (they have urged the UK government to reach a frictionless trade deal as soon as possible).
Stockpiling incurs higher holding costs:
The moment a business moves from a just-in-time supply chain back to a just-in-case system, their storage costs increase. Everything a business sells or manufactures now has to be sold as quickly as possible, as the margin on each good sold is constantly being eaten away by the rental costs for stock left sitting on the shelf. Goods need to be sold as soon as possible, before the cost of storage outweighs the chances of making back the initial investment.
Stockpiling drains cash flow:
Storage costs aren’t the only way that stockpiling can drain on a business’ cash reserves. By spending extra money on goods before those goods are ready to be sold and paid for, the short-term expenses of that business increase faster than its income. This is a serious issue for competitive businesses running on tight margins — so much so that it may be safer to avoid stockpiling and factor in the risk of logistical delays and new import-export costs. It depends on the type of business you’re in, and what our governments choose to do with customs tariffs from 29th March 2019.
Will customs tariffs increase overnight?
The UK imports 40% of the food it consumes, so there are good reasons for the British government to protect frictionless trade with Ireland and mainland Europe. We’re also hopeful that the UK government will take just as long to discuss and implement new food tariffs as it has to discuss and negotiate Brexit. Our hope is that customs tariffs will not materialise for a number of years, but we will have to wait until the UK’s first post-Brexit budget, and the subsequent budgets of Ireland and other EU member states, to be sure.
How Baku are preparing:
At Baku, we have modelled alternative routes and we’re monitoring customs declarations on both sides of the border to reduce the uncertainty for our clients wherever possible. We have also applied for Temporary Storage Facility status at our Rosslare warehouse, so that goods crossing the border can be stored for up to 90 days while they await customs clearance. Find out more about our Brexit Preparations.